BUILT TO LAST
BUILT TO LAST
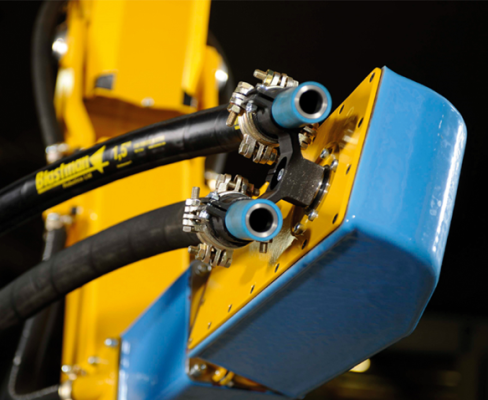
This blog discusses the wear of blast cleaning equipment during the process. Blast cleaning is an effective way of surface finishing old and new products and parts. Blast cleaning is typically done by accelerating abrasive particles through a nozzle towards a workpiece by mixing them in an airflow. High-velocity particles impact the workpiece causing erosion on the surface. After impact, the particles will inevitably rebound. Rebounding particles can then cause wear on blast cleaning equipment.
Wear conditions are very random due to the random rebounding of the particles. There are three key characteristics that should be considered when thinking about rebound: Impact angle, nozzle distance, and abrasive shape. The impact angle of the rebounding particles varies due to the alternating surface shape and blasting angle, so it is highly unpredictable. The distance of the nozzle determines the kinetic energy a particle has after impact with the workpiece, which is a key factor when determining the wear amount. This fact suggests that blasting the workpiece from as far away as possible would reduce wear in equipment, but after a certain point, increased distance reduces the efficiency of the process. Therefore, equipment should be designed so that having the nozzle close to the workpiece surface won’t cause excess wear on the equipment itself.
Some particle shapes are more prone to rebound. A round “shot” particle stays intact after the impact, resulting in a more profound rebound. A sharp-cornered “grit” particle breaks more easily upon impact, resulting in a more random rebound behavior and increased loss of kinetic energy. Overall, wear in the blast cleaning equipment depends on multiple factors, of which most are random and unpredictable. One thing is for sure, the rebound will happen and it will cause wear on blasting equipment.
Even though rebound is inevitable, it is possible to reduce wear by proper design and using wear-resistant materials. One option is to coat the equipment with a wear-resistant material. The material often used for this purpose is polyurethane, which is durable and known to absorb energy well.
A second solution is to find a suitable material for the equipment itself. Steel manufacturers produce a variety of different steels for customer needs. The most important features for the equipment material are hardness, toughness, and fatigue resistance. Structural steels are known to be tough but usually lack hardness. Steels with high toughness as well as hardness are called wear-resistant steels. For the material to properly withstand abrasive wear, hardness should be near the hardness of the abrasive particles used in the process. A thumb rule is that the hardness of the equipment should be at least 0.8 times the abrasive hardness. High-end wear-resistant steels have a hardness close to the hardness of common steel particles used in blast cleaning and are suitable to be used for most equipment. The diagram below shows how to wear in steel plates caused by blasting is reduced by the increase in equipment material hardness.
Abrasion loss in steel plates after blasting
Despite being hard and tough, machining and welding of wear-resistant steels are easy with the right manufacturing equipment. Wear-resistant steel is more expensive than basic structural steel but savings are expected in the long run. Savings are achieved by avoiding replacing parts of the equipment and reducing the need for maintenance. Using wear-resistant steel also allows the manufacturing of lighter equipment, since thinner steel can be used.
Blastman robots are often used for blast cleaning large structures and the process can last for long periods of time. Due to this, it is particularly important that the equipment is made of durable materials and functions reliably in these conditions. Here at Blastman Robotics, we have devoted considerable resources to determining the best possible materials for our robots. This allows for a long lifetime of the equipment, fewer maintenance costs, and an increase in reliability.
Sakari Veijola
Sales & Marketing Director
Blastman Robotics Ltd
You might be interested in these articles
Company News Events
03. Mar 2025
Welcome to visit us at MECSPE, Bologna from March 5th to 7th.
Blog Posts Company News Events
16. Dec 2024
Season´s Greetings from Blastman Robotics Ltd
Company News Events
23. Aug 2024
BLASTMAN AT INNOTRANS 2024
Blog Posts Company News Events
22. Aug 2024
ABRASIVE BLASTING INVALUABLE FOR RAIL INDUSTRY
Company News Events
20. Jun 2024
BLAST CLEANING LARGE STEEL STRUCTURES FOR ENERGY INDUSTRY
Company News Events
20. Feb 2024
WE´RE EXHIBITING AT PAINTEXPO 2024
Blog Posts Company News Events
18. Dec 2023