Flexibility is the key
FLEXIBILITY IS THE KEY
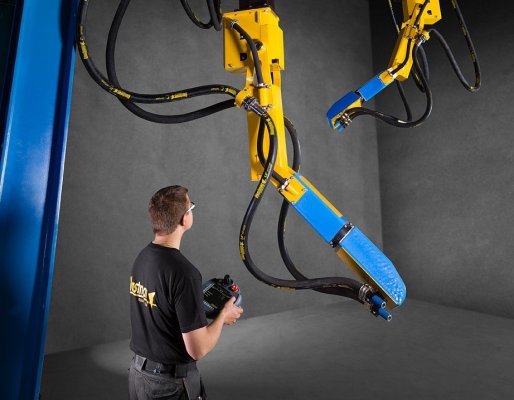
Short processing times and a reproducible, high-quality production process are due to rising customer requirements increasingly decisive to set oneself apart from the competition. Demand-oriented blasting robots that offer a high degree of flexibility meet these requirements and increase workplace operating comfort and safety.
On the occasion of the modernization of the blasting chamber of a manufacturer of maritime cranes to expand production capacity Blastman Robotics developed a new blasting robot. The special feature: it has a quick-coupling device with which the control cabin of the blasting robot can be replaced by a manlift.
Fig. 1: Blasting robot with a separate control cabin.
Quick-coupling device
Blasting robots with such a quick-coupling device can be used extremely flexibly. For example, they can be used for individual and special components or also workpieces for which no CAD data are available, with the help of the control cabin in manipulator mode. The operator cleans the component by manual control. It is possible to create blasting programs for the respective components using the so-called teach-in procedure. All movements and functions of the system are recorded and can be accessed and used at any time for similar components.
Fig. 2: Platform for replacing the control cabin with a manlift.
The operator can control the blasting robot comfortably from the cabin, which is protected from the harmful environment in the blasting chamber. The control is very simple via a touch screen and two joysticks, as is common today with many machines and systems. The control cabin is well-insulated and fully air-conditioned and is operated at a slight overpressure to prevent noise and dust from entering.
Fig. 3: Comfortable control from the cabin.
Portable control panel
The sequences for geometrically simple components can be created very quickly and efficiently with the portable hand panel. The robot's movements are stored in the point-to-point process, which leads to very efficient blasting programs. In addition, the hand panel can be used for modifications and adaptations of existing blasting programs if the current component geometry or position deviates from the programmed version. During maintenance and servicing work, it is also used for controlling and checking the function of the blasting robot.
Fig. 4: Easy operation with the handheld panel.
Automatic program generation
All Blastman fourth-generation blast robots include offline programming software developed explicitly for blast robots, with automatic program generation from the CAD data of the component and the blast chamber. In this way, a large part of the individual program sequences is already created and only needs to be supplemented by the component and customer-specific parameters - such as the actual contamination present and the desired degree of cleanliness of the component.
The integrated simulation tool - which visually displays the robot's movements and the blasting process as a 3D model on the screen - also identifies possible collisions. In addition, the cleaning processes are already optimized offline in terms of quality and time without having to interrupt production. The new blast robots can thus be integrated very easily even into existing blast chambers and ensure optimum blast cleaning performance, which significantly improves the costs and economic efficiency of blast processing.
Flexibly usable
In automatic mode, the blasting robot performs its work by repeating the saved work sequences. This reliably leads to reproducible cleaning results. If some areas such as undercuts or shadow areas of the component are not reached by the blasting robot, the control cabin can be uncoupled from the telescope of the gantry bridge and replaced by a manlift for manual blasting work. Since this working platform can reach every angle of the blasting chamber thanks to the portal bridge and the rotating telescope, it can also be used for inspection and quality control. This is particularly advantageous for very large components, as no complex scaffolding or turning of the components is required.
Heiko Reski
Sales Manager
Blastman Robotics Ltd
You might be interested in these articles
Company News Events
03. Mar 2025
Welcome to visit us at MECSPE, Bologna from March 5th to 7th.
Blog Posts Company News Events
16. Dec 2024
Season´s Greetings from Blastman Robotics Ltd
Company News Events
23. Aug 2024
BLASTMAN AT INNOTRANS 2024
Blog Posts Company News Events
22. Aug 2024
ABRASIVE BLASTING INVALUABLE FOR RAIL INDUSTRY
Company News Events
20. Jun 2024
BLAST CLEANING LARGE STEEL STRUCTURES FOR ENERGY INDUSTRY
Company News Events
20. Feb 2024
WE´RE EXHIBITING AT PAINTEXPO 2024
Blog Posts Company News Events
18. Dec 2023