THE FUTURE OF ABRASIVE BLAST CLEANING
BLAST CLEANING IN THE SPEARHEAD OF AUTOMATION – THE FUTURE OF ABRASIVE BLASTING
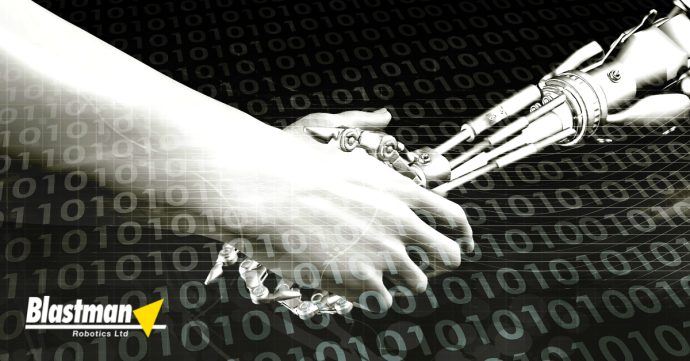
From the get-go, Blastman Robotics has represented the cutting edge of robotic abrasive blast cleaning. Blastman designed and manufactured the first robot for the job and was also the first to develop hydraulically operated robots into servo robots. Additionally, it was the first company to develop an offline programming tool specifically for abrasive blasting – the Blastman Studio. It is also the first company to build equipment capable of handling objects ranging from rail wheelsets to workpieces with a length of hundreds of meters, a height of 12 meters, and a width of 30 meters.
Achieving all this still doesn't mean abrasive blast cleaning has reached its ultimate developmental peak. On the other hand, it doesn't mean the industry is fading away, either. In fact, chances of that happening are highly unlikely. Instead, the question to ask is, how will abrasive blasting evolve?
When this is examined from Blastman's point of view, there are two interlocking factors: the further development of the company's own robotics and how it connects to Industry 4.0. What kind of steps will Blastman and abrasive blasting as an industry take? To cover this, we'll be going through the following topics.
1. Why develop abrasive blast cleaning further?
2. Blastman is not alone in developing abrasive blast cleaning
3. Future of abrasive blasting serves customers
4. Fully automated blast cleaning process
5. Scanning and machine vision essential for the future of abrasive blasting
6. More efficient production with automated maintenance notifications
7. Even neater results in the future of abrasive blasting
8. Blastman is the future of abrasive blasting
Why develop abrasive blast cleaning further?
The use of robotics can easily create the impression that a process has been developed to its extent when it's often only one of the first steps toward automation. In fact, the next ten years will most likely prove pivotal in the further automation of painting, welding, material handling, and practically any industry where robots are already in use. We are constantly getting closer to human-independent production.
Although some see this as a negative trend, a human-free environment is one of the sustaining ideas behind Blastman's solutions, and for a good reason. As abrasive blast cleaning, especially in a blasting room, is grueling and dangerous work, utilizing robotics for the job is, more than anything, a matter of work safety and one of Blastman's core values.
Not to worry, though, through the need for maintenance, measurement, monitoring, and adjustment, humans will never disappear from the picture but are freed to operate safely outside the process. At the same time, as the autonomy of robots and automation of the blast cleaning process are developed further, higher production efficiency is reached through elevated speed, accuracy, and consistency as well as versatile flexibility regarding the size and shape of workpieces.
This, in turn, is important for the benefit of the ever-greater result, as no less than 70 % of paint surface degradation is due to a poor blasting job. The better the surface quality, the better the paint or other coating adhesion. This translates to better corrosion protection and a higher lifetime of the end product, resulting in less environmental burden.
Blastman is not alone in developing abrasive blast cleaning
Even though Blastman Robotics has its roots deep in the history of blast cleaning robotics and possesses a unique reserve of experience and know-how, the company sees benefits in cooperation. It works closely with, for example, the University of Oulu, universities of applied sciences and Finland’s national research institute, VTT.
A great example of fruitful cooperation is a thesis determining the most durable steel option for the arm of Blastman's latest generation of robots. Creating opportunities for students to develop their expertise and benefit society, and in return, facing the future even stronger through innovations and excellent employees is a mutually beneficial outcome Blastman gladly supports.
However, the one thing that everything culminates on is Blastman's cooperation with its customers. After all, they are the ones who end up using the equipment and solutions. The feedback Blastman gets from this cooperation is not only invaluable for the future development of abrasive blasting but also gets channeled back to the end users as more sophisticated equipment, solutions, and services.
Future of abrasive blasting serves customers
Blastman's closely-knit relationship with its customers means that the future of abrasive blasting goes hand-in-hand with the development needs of different customer segments and the economic cycle they experience. An illustrative example is the green transition and the resulting spike in wind power demand.
For Blastman, the high demand for wind turbines has proven to be a part of a trend of growing workpiece sizes. The company has acted accordingly and has finalized the design of its largest bridge, enabling 32-meter-wide gantries for its robots. To give perspective, that means an actual ship and few companies can even make a crane this wide. To go along with this, Blastman is the only company in the world that can manufacture 10-meter telescopes for robotic abrasive blasting.
In addition to the demands concerning ever-larger workpieces, the wind power sector has driven Blastman to develop its ability to provide solutions for blast cleaning the interior surfaces of tower sections. This is another great example of how, as a part of its ongoing operations, Blastman is modifying its equipment and manufacturing new solutions to meet the needs of its driving force in product development, and its expanding customer base. While it's customer service in real-time, it's also an investment in the future of abrasive blasting.
Fully automated blast cleaning process
When thinking about a future scenario, it is easy to overlook the gradual stages between now and then. For example, it is possible to imagine a manufacturing process running entirely independently. Still, it's not like such a facility is simply a vision until it's one day built. It happens step by step.
What is especially exciting is that many of these steps have already been taken. Numerous solutions needed for abrasive blast cleaning to operate as a fully autonomous cell are under constant development, and the first versions of these solutions are already being put to use.
Any automation process can be summarized into three simple steps: Material goes in, material is processed, and material goes out. In a fully automated process, all three steps are autonomous, with machines working (and discussing) with each other. Material transport, meaning the entry and exit of workpieces in blast cleaning, has already been automated in many industries. This solution already exists, but what is really interesting is the stuff that happens in the processing stage. More on that next.
Blastman B20S robot in blasting chamber
Scanning and machine vision essential for the future of abrasive blasting
After the workpiece has entered the blast cleaning process, a fully automated system would either need to identify the workpiece or create a 3D model on which the process would be based. Many of Blastman's customers have 3D models ready, which can be easily used to create blast cleaning programs and identify the pieces entering the process.
If a model doesn't exist, things get more interesting, and the model needs to be created. For this purpose, an automatic system would scan the object like pieces are scanned in automation, or other industries today. This would produce a 3D model on which a blast cleaning program – the so-called “scan-to-blast” process – could be created.
Creating a 3D model manually can be time-consuming and poorly suited to production. To develop a scan-to-blast solution in 3D and in its own environment, Blastman is working with scanning, measuring, and machine control companies. The future will be more and more about reconciling these sectors.
Machine vision and 3D cameras can also be used for other purposes, such as identifying which piece has entered the treatment and how it is positioned. This way, the piece's placement doesn't have to be exact. If the object deviates from the programmed location, the machine vision will detect the actual location and relate the information to the robot, which will then adjust the program accordingly. This kind of solution is already in use but is also being developed further.
Passenger coach blasting with Blastman Studio
More efficient production with automated maintenance notifications
When the solutions are in use, one of the ways to elevate automation is to develop predictive maintenance. One of Blastman's goals towards a more automated blast cleaning process is getting its maintenance as predictable, need-based, and customer-specific as possible.
Maintenance routines vary depending on usage and significantly affect the ability to control and schedule the use of resources. When it comes to automation, this requires a large number of measurement points, but also machine learning. In practice, the system tracks data about the robot and processes it independently to generate actions, reminders, and instructions.
If, for example, a customer's blasting hose starts to wear out, the system gives out an alert on an impending replacement need. Suppose the interval drops and the previously measured value is not reached. There could be too much dust, or the hose supplier has changed, and the hose is simply of lesser quality. The workpiece and the program also affect the wearing. In these cases, an automated system can inform that the hoses are wearing out faster than before or change the wear time indication to a shorter interval. This method is already implemented for all crucial wear parts of the Blastman system and will be extended to cover the entire system.
Even neater results in the future of abrasive blasting
After a surface has been cleaned, it becomes available for quality control. On a path toward a fully autonomous blast cleaning process, this would mean an automatic online measurement of cleanliness, roughness, and overall surface quality. If the online quality check reveals that a particular spot of the surface needs more work, it would then automatically create a program for the robot to execute the necessary additional treatment.
To package things up, a complete autonomous blasting process would also automatically gather all data generated. A report would then be formed and sent, among others, to production control, quality control, operators, and the maintenance team. Finally, the report would be tailored to the customer's preferences to allow further optimization of production.
Blastman is the future of abrasive blasting
Blastman has always been a technological driver. In fact, it's in its lifeblood. That is why the company also bases its future on its role as a frontrunner. In developing its own equipment and solutions, the company takes different environments into account and adapts accordingly.
In the broad picture, Blastman is monitoring the market and technological advancement and planning how to combine things to benefit the whole future of abrasive blasting. By bringing forth automation and monitoring options, it aims towards autonomous blasting cells and tapping into Industry 4.0, getting a little better and closer every day.
The combination of its long history, special know-how, and curiosity towards the future will no doubt maintain its position as the leader of its field. Blastman's robots took over the abrasive blasting industry a good while back. To prevent any concern, the company aims to keep its robots attached to rails in the future, too, so they don't take over the world!
You might be interested in these articles
Company News
03. Apr 2025
BLASTMAN BLAST CLEANING ROBOTS IN DIFFERENT INDUSTRIES
Blog Posts Company News
01. Apr 2025
BLASTING ROBOTS PROMISE EFFICIENCY
Blog Posts Company News
13. Mar 2025
SUPPORTING GROWTH WITH AUTOMATED BLASTING
Company News Events
03. Mar 2025
Welcome to visit us at MECSPE, Bologna from March 5th to 7th.
Blog Posts Company News
12. Feb 2025
ROBOTIC ABRASIVE BLASTING IS AN EASIER CHOICE THAN YOU MIGHT THINK
Blog Posts Company News
22. Jan 2025
LEADING THE FUTURE OF ROBOTIC BLASTING
Blog Posts Company News Events
16. Dec 2024