BLAST CLEANING OF TRANSFORMERS
BLAST CLEANING OF TRANSFORMERS
Case: CHONGQING HITACHI ENERGY TRANSFORMER, Chongqing, China
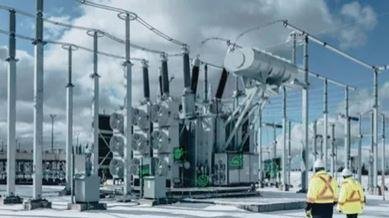
Hitachi ABB Energy Chongqing is a global leader in transformers, offering liquid-filled and dry-type transformers. Hitachi Energy's power transformers are key components in power networks.
BACKGROUND
ABB transformer, as the predecessor of Hitachi ABB, had used Blastman robot for automatic sandblasting of its transformer cases at the Ludvika factory in Sweden since the late 80s in the last century. In 2023, the successful blast robot experiences of the Ludvika project were replicated in Hitachi ABB Chongqing, one of the automatic manufacturing plants in Asia. Hitachi ABB Chongqing has applied Blastman latest generation automatic robot for automatic sandblasting to transformers.
Blastman B16XS robots Blastman B20CS robot
OBJECTIVES
The requirement was to blast clean automatically and completely exterior surfaces and essential interior surfaces of various transformer cases and accessory workpieces at a given speed.
SOLUTION
We delivered two sets of robotic blast rooms with two different models of robots. The first blast room is equipped with one Blastman B20CS robot. The robot arm is equipped with two 16 mm blast nozzles.
The second blast room, which is equipped with two sets of B16XS robots with one 16mm nozzle on each robot is designed for blasting accessory workpieces mounted on the transformers.
Blastman Studio software allows operators to make blasting programming off-site and meanwhile improves the availability and efficiency of the robots dramatically for each different workpiece
B20CS TECHNICAL INFORMATION
Nozzle diameter | 16mm |
Number of nozzles | 2 |
Blasting pressure 7 bar | 7 |
Blasting rate | 75 m2 per hour |
Abrasive | Steel grit |
Degrees of freedom | 8 |
Programming | Offline / Point-to-Point |
Operation mode |
Automatic, Manipulator mode |
B16XS TECHNICAL INFORMATION
Nozzle diameter 16 mm | 16mm |
Number of nozzles/robot | 1 |
Blasting pressure | 7 bar |
Blasting rate/robot | 50 m2 per hour |
Abrasive | Steel grit |
Degrees of freedom | 7 |
Programming | Offline/Point-to-Point |
Operation mode | Automatic |
RESULTS
Thanks to the robots, the required roughness and cleanliness were reached in both two lines in the required cycle time. High efficiency and constant quality were guaranteed by using Blastman robots.
Compared to traditional manual blasting that requires massive manhours and manpower, programmed Blastman robots have simply reduced a large amount of labor force, only very limited manual work is required for the blast cleaning process as a result. Operator safety is always a key concern.
Blastman robots, running automatically, ensure the protection of operators and remove them from the harsh blasting environment.
You might be interested in these articles
Company News
03. Apr 2025
BLASTMAN BLAST CLEANING ROBOTS IN DIFFERENT INDUSTRIES
Blog Posts Company News
01. Apr 2025
BLASTING ROBOTS PROMISE EFFICIENCY
Blog Posts Company News
13. Mar 2025
SUPPORTING GROWTH WITH AUTOMATED BLASTING
Company News Events
03. Mar 2025
Welcome to visit us at MECSPE, Bologna from March 5th to 7th.
Blog Posts Company News
12. Feb 2025
ROBOTIC ABRASIVE BLASTING IS AN EASIER CHOICE THAN YOU MIGHT THINK
Blog Posts Company News
22. Jan 2025
LEADING THE FUTURE OF ROBOTIC BLASTING
Blog Posts Company News Events
16. Dec 2024