BLASTING ROBOTS PROMISE EFFICIENCY
BLASTING ROBOTS PROMISE EFFICIENCY
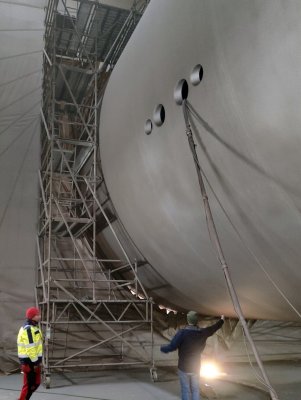
At a time when resource efficiency and digitalization are becoming increasingly important, efficient technologies such as blasting robots in intelligent blasting chambers are proving to be part of the solution to these problems.
Automated blasting prior to coating is essential to meet the ever-increasing demands for energy savings and automation, including Industry 4.0, in the pretreatment of large components. Blasting robots specially designed for this process and integrated into intelligent blasting chambers offer the ideal solution.
Manually blasting large steel components such as wind turbine towers is hard work; in comparison, the fully automatic robotic blast cleaning of the huge parts saves a lot of time and energy.
Blasting as a bottleneck
Manually blasting large steel components is hard work that demands a lot from employees. Extreme physical strain as well as noise, heavy protective clothing, and air enriched with unhealthy dust define the working environment. The blasting workers often have to blast large steel components for a very long time on simple scaffolding or in an awkward
overhead position. For example, a manufacturer of towers for wind power plants currently processes a segment of 34m in length and 7.6m in diameter per day. Only for the manual blasting of the outer surface of these tower segments, two complete shifts with four blasting workers each are required. That’s a total of eight man-days. These enormous personnel costs, combined with the high physical demands, make it increasingly difficult for companies to find employees willing to perform this work, even though above-average wages are paid. As a result, the blast cleaning of large steel components is increasingly becoming a bottleneck in production for many companies.
A wall-guided blasting robot equipped with two large blasting nozzles and 8 to 10 bar blasting pressure performs this work fully automatically within 4 hours. This significantly faster processing means that both the ventilation and abrasive reclaim system are in operation for a considerably shorter time. In addition, a blasting robot does not require lighting or an air-conditioned environment. This saves a total of 1200 kWh of energy per tower segment, which, of course, also helps the environment. However, blasting robots not only make surface preparation faster and cheaper, they also make it safer and ensure a consistently higher quality. In order to be able to automatically carry out the even more laborious blast cleaning of the interior surfaces of wind turbines in the future, Windar Renovables is currently testing a robotic concept developed by Blastman Robotics. In addition to the above-mentioned advantages of facilitating work and saving energy, this robotic concept can also take over the automatic application and return of the abrasive after blast cleaning.
Another example of an application in the wind energy sector is the blast cleaning of the rotor hubs that connect the rotor blades to the nacelles. These rotor hubs are currently cast with diameters of over 8m and then have to be cleaned in the fettling shop to remove centimeter-thick layers of casting sand, which is extremely laborious to do manually, especially on the inner surfaces.
The first blasting robots are already being used by shipyards to blast clean ships and barges for the installation of offshore wind turbines. Since very large areas also have to be pre-treated here before coating, the use of special blasting robots is particularly effective. Mobile blasting robots move under the hulls to blast them clean. Manually, this is only possible with very strenuous and time-consuming overhead work. The upper and side surfaces of these barges are processed in parallel by blasting robots that reach every area of
The blasting chamber is accessed via gantry bridges, so that a significant time and energy saving is achieved here as well.
Robotic blast cleaning of a wind turbine rotor hub
Intelligent blast chamber
Intelligent blast chamber. Blasting robots can be programmed offline on a PC using the digital component data. The CAD files for the components can be easily imported into the 3D environment of the programming software. Optimal blasting distances and angles for the blasting robot are then automatically generated based on the component geometry and its position using inverse kinematics, and can then be checked using the integrated simulation software. A so-called Smart Blastroom is an ideal environment for a blasting robot. As an intelligent blast chamber, it enables complete control and monitoring of the entire blasting process. All the equipment and all the functions of the blast chamber are
integrated into a central control system, with the entire blasting process being visualized and monitored via the uniform user interface. This enables both rapid error detection and predictive maintenance recommendations, resulting in high system availability through reduced downtime and, at the same time, extending the service life of the equipment. The central control system can also use frequency converters to control the ventilation and blasting media processing systems based on capacity usage and demand, and to monitor the status of the dust filters and the filling level of the blasting media silo using sensors. Automatic refilling ensures consistent blasting media quality and thus reproducible blasting results.
MES connection
Blasting robots and the blast chamber process parameters, such as energy and abrasive consumption, are recorded in logs and are available in digital form for quality assurance and operational production management for production planning and control. This means that processes can be continuously monitored and improved to further optimize the efficiency of blast cleaning as a whole.
Author
Heiko Reski
Sales Manager
Blastman Robotics Ltd, Düsseldorf (Germany)
heiko.reski@blastman.com
The article was published in IST - International Surface Technology 18 (2025) issue 1, p. 40-41. Available online at: https://www.springerprofessional.de/link/50770488
You might be interested in these articles
Company News
03. Apr 2025
BLASTMAN BLAST CLEANING ROBOTS IN DIFFERENT INDUSTRIES
Blog Posts Company News
01. Apr 2025
BLASTING ROBOTS PROMISE EFFICIENCY
Blog Posts Company News
13. Mar 2025
SUPPORTING GROWTH WITH AUTOMATED BLASTING
Company News Events
03. Mar 2025
Welcome to visit us at MECSPE, Bologna from March 5th to 7th.
Blog Posts Company News
12. Feb 2025
ROBOTIC ABRASIVE BLASTING IS AN EASIER CHOICE THAN YOU MIGHT THINK
Blog Posts Company News
22. Jan 2025
Leading the Future of Robotic Blasting
Blog Posts Company News Events
16. Dec 2024