BLASTMAN BLAST CLEANING AND PAINTING FACILITY
BLASTMAN BLAST CLEANING AND PAINTING FACILITY
JSC Belaruskali, Salihorsk, Republic of Belarus
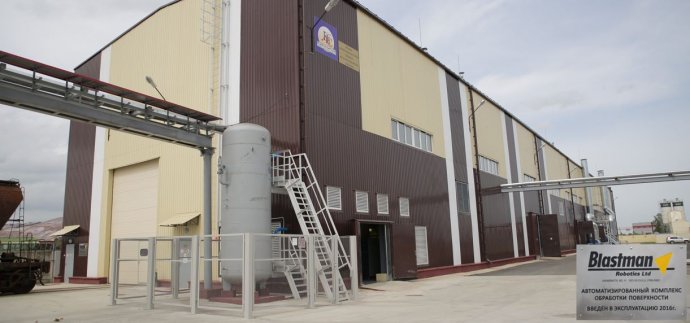
The requirement was to blast clean and paint completely exterior and interior surfaces of various hopper cars with a given speed of 720 cars per year.
JSC Belaruskali is one of the world’s biggest producers and exporters of potash fertilizers. According to International Fertilizer Association, it accounts for the seventh part of the world's potash production and export to more than 90 countries.
The Blastman surface treatment line for freight cars includes a pre-drying chamber, robotized blasting chamber, priming, and top coating painting chambers, equipped with painting equipment, as well as a transport system of the cars and compressor station. The surface treatment line provides fast and effective cleaning and painting of the old freight cars with reliable and faultless quality. In the pre-drying chamber, the car is drying from the rain or snow, and it's prepared for the following process phases. In the blasting chamber, Blastman B20C-S robot blast cleans efficiently all exterior and interior surfaces with superior blasting quality. In the painting chambers primer and coatings are applied. The curing of paint is sped up by heating the room up to 60 C degrees. In the marking chamber, cars are marked and quality inspected.
Technical information
Nozzle diameter | 16 mm |
Number of nozzles/robot | 2 |
Blasting pressure | 7 - 8 bar |
Blasting rate | 70 – 100 m2/h |
Abrasive | Steel grit |
Degrees of freedom | 8 |
Programming | Offline and Point-to-Point |
Operation mode | Automatic |
PRE-DRYING CHAMBER
The pull winch moves wagons into the pre-drying and blow-off chamber, where water, snow, and ice are removed.
Powerful calorifiers located along the chamber ceiling use warm air from the compressor unit and the hot steam on the heating system.
Wagons are prepared for further processing here. If they are to be cleaned and painted in their own wheelsets, it is necessary to protect the hydraulics and other vulnerable spots.
After the drying cars are moved into the blasting chamber, where the surface is cleaned from rust and old paint.
ROBOTIC BLASTING CHAMBER
Advantage of Automated Blast Cleaning
- desired surface cleanliness and roughness
- slight surface shaping by controlling the blast pressure
- working lifts and platforms not needed
- freedom to use any abrasive material
- considerable savings in production costs
- increased production capacity
- remarkable health and safety implications
The blasting chamber is equipped with the gantry-type robot Blastman B20CS with a separate control cabin for the possibility to control a robot in manual mode.
The robots are equipped with powerful nozzles providing superior blast cleaning efficiency and quality. The flow of compressed air through flexible hoses to the nozzles carries the abrasive. This solution enables the robot head to perform rotational movement around its axis and blast clean railcar all around its surfaces including interiors of hopper cars.
Blastman continuously operating double chamber blast pot is specially designed for nonstop robotic operation.
Robots Blastman is also designed in a way that allows to clean the internal surfaces of hopper cars.
PRIMING AND TOP COATING PAINTING CHAMBERS
Primer and top coating painting chambers are equipped with a man lift designed for the painting environment. Man lifts are moving in three directions and provide easy access to all surfaces of the car.
Painting performed by airless spray with high pressure in an electrostatic field. Through the paint mixing unit paints fed by the high-pressure hoses from the warehouse directly to spray guns. The control unit continuously monitors the proportion mix of the paint and solvent and also considers the number of connections of volatile organic compounds (VOC) during the painting.
The painting chambers are also designed for drying painted wagons, in this case, the maximum temperature in the chamber reaches + 60 ° C. The chamber comes with air conditioning, equipped with an automatic device of heat accumulation. The efficiency heat accumulation rate is 70%.
Replacement air is taken outside the chamber. Air is filtered before heating. Located on the ceiling air duct channels evenly distributed air throughout the chamber. Exhaust air is sucked into the painting exhaust fan filters through the floor and diverted to the outside.
MARKING CHAMBER
The last process phase is applying the application of signs and inscriptions in the marking chamber. The marking chamber is equipped with an air conditioning and heating system and automatic adjustment of heat.
For the convenience of applying the marking signs to the surface of cars, the chamber provided with mobile platforms, which are controlled by pneumatic cylinders and motors.
After the car leaves the surface treatment line, it is ready for long-term
use of the carriage of goods.
You might be interested in these articles
Company News
03. Apr 2025
BLASTMAN BLAST CLEANING ROBOTS IN DIFFERENT INDUSTRIES
Blog Posts Company News
01. Apr 2025
BLASTING ROBOTS PROMISE EFFICIENCY
Blog Posts Company News
13. Mar 2025
SUPPORTING GROWTH WITH AUTOMATED BLASTING
Company News Events
03. Mar 2025
Welcome to visit us at MECSPE, Bologna from March 5th to 7th.
Blog Posts Company News
12. Feb 2025
ROBOTIC ABRASIVE BLASTING IS AN EASIER CHOICE THAN YOU MIGHT THINK
Blog Posts Company News
22. Jan 2025
Leading the Future of Robotic Blasting
Blog Posts Company News Events
16. Dec 2024