ENSURING WORK SAFETY IN AUTOMATED ABRASIVE BLASTING - A SAFETY MEASURE IN ITSELF
ENSURING WORK SAFETY IN AUTOMATED ABRASIVE BLASTING - A SAFETY MEASURE IN ITSELF
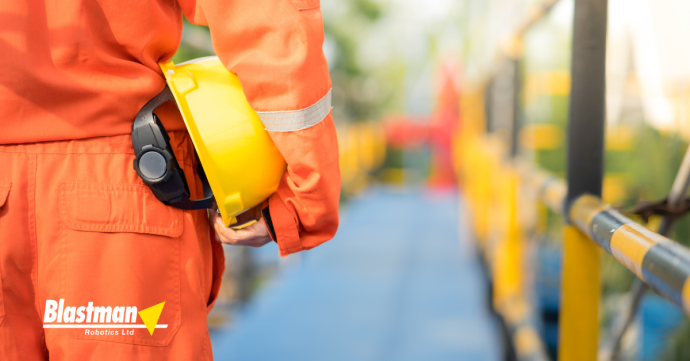
Spearheading the development of industrial automation, especially automated abrasive blasting isn’t something one could do without work safety closely in mind. In the case of Blastman Robotics, there’s a dual aspect. In its product and solution development as well as customer service the company pays close attention to work safety. On the other hand, its whole concept of automated abrasive blasting is based on a matter of occupational safety. So much so that it goes back to the roots of the company.
Automated blasting started with work safety
In the early 1980’s the Finnish heavy industry company Tampella had a lot of problems with its abrasive blasting station. Challenges with occupational safety and well-being, such as respiratory symptoms and arthritis, eventually led the doctor of the factory to urge the management to invest in a solution that would free the workers from operating inside the blasting station. This led to the development of a robot capable of operating in challenging conditions inside the blasting chamber.
After the acquisition of the robotic operations of Tampella by the famous Finnish steel mill, Rautaruukki, and their eventual separation through the formation of Blastman Robotics it is safe to say that for Blastman it all started with work safety.
The success of Blastman naturally has a lot to thank for the tireless repeatability, uniform quality, and excellent efficiency enabled by its method and solutions but what is truly noteworthy, is that it is all grounded in the willingness to ensure safer and healthier working conditions. To this day the most central agenda of Blastman Robotics is to bring the people out of the blasting camber.
Automated blasting by the book
Blastman’s technology is in itself a way to tremendously develop the safety of an industrial abrasive cleaning process. However, taking care of work safety doesn’t end there, and the safety during use is not to be forgotten. In its product development and implementation of its equipment for customers, Blastman follows all the directives, laws, and other set requirements governing its solutions and their use.
Work platforms, robots with a cabin, or other equipment classified as man lifts have to go through all the necessary calculations of their own and have to receive type approvals that Blastman obtains for specific markets, such as the EU and the US. This is a process that cannot only be done by the company itself and for this it uses external inspection and certification specialists with the capability to grant the approvals according to the distinctive regulations of different countries. This way Blastman can give out its declaration of conformity for all manufactured products.
In recent years Blastman has completely redesigned its manuals with great effort and much of them is devoted to the safe use of the equipment. Additionally, sections about keeping the equipment in working order can be valued from a safety point of view. Even well-designed high-quality equipment needs maintenance, and the better it’s taken care of the safer it is. For this reason, Blastman has emphasized preventive maintenance not only in the manuals but more importantly in the equipment itself. Blastman systems notify the operator proactively about preventive maintenance so that important actions are not forgotten.
Taking work safety further
Bluntly put, directives and certificates are only pieces of paper unless they are not internalized and reflected in the actions. To do things responsibly and correctly, as they should be, requires quite a lot of understanding. When mechanics, electrics, and software are at play all at once, ensuring the safety of the process requires knowledge of all the areas. Education is not enough, but experience, know-how, and understanding of what the directives entail are needed as well.
Whenever equipment is designed at Blastman, there is a team at work that uses risk analysis and other necessary failure analyses to identify all possible situations and to ensure the equipment is safe to use – and not only for its actual operators but also for people who are not familiar with the process and robot operation. For Blastman this entails more than simply adding dos and don’ts in a manual but instead actually basing the design of the equipment as much on operator safety as the blasting performance. This requires the use of safety-rated equipment and specially designed, sometimes customer-specific, solutions to be created.
Automated blasting, automated safety
To ensure safety during the use of its equipment Blastman has put in place mechanisms to prevent dangerous situations resulting either from abuse, neglect, or accident. All of this is controlled by a state-of-the-art safety system that monitors all operations, stops actions, and prevents restarts if necessary.
The most demonstrative examples of safety functions are actions that cause the system to stop. These include opening any door during the blasting process or pushing an emergency stop button. Both of these actions bring the whole installation to a safe state which also includes de-pressurizing the blast pot and in case of e-stop, to shut down all actuators in motion. In addition to the above standard safety functions, Blastman has created a range of other measures, which increase safety and give peace of mind to operators and maintenance personnel. As an example, operators can disable blast cleaning from the user interface at any given time.
Blastman systems also always have a switch to determine the appropriate operation mode. With this, the operator can select between service, manual blasting, or automated blasting modes. Each mode changes the functions of the safety system to allow only the use for the intended purpose. Blastman also builds specific operation modes according to customer needs. Each of these custom modes is designed according to the same strict safety standards and culture of Blastman.
Blastman takes into account more than the safety of its solutions
Residual risks, the risks whose prevention can’t be built in, are featured in the manuals and on all necessary signs in the operating areas. One such matter is a reminder to always make sure the blasting chamber is empty of people before the continuation of the blasting process. Risks are also minimized with good guidance and training as Blastman organizes its customers an extensive training focused on safe and efficient use and maintenance. The key point is to make the chamber and the process as safe for people as possible.
In projects where a robot is installed into an existing line, all other factors that affect the process are taken into account and integrated under the same entity where Blastman’s safety system is the safety master of the area. In practice it means that existing safety functions and PLCs are connected to Blastman system to ensure that safety stops from Blastman stop existing equipment and vice versa. Also, connections related to operation modes are made, such as connecting old manual blast pots to allow them to work only when the correct mode is selected.
Work safety is an integral part of customer-satisfying automated blasting
When it comes to the implementation of the safety features of the blasting process, there is often no need for custom measures as the most usual features such as emergency stop integrations and door limits are delivered as standard. Even though most of the customer cases can be handled with standard solutions Blastman’s professionals are no strangers to tailoring and have a lot of experience in design and analyzing. Customer-specific workpiece transporting solutions that are in operation in or around the blasting process can just as well be taken into account.
The well-designed and functional safety features of Blastman’s solutions have gathered great feedback from customers but the company gets even more praise for the way its automated robotic solutions can turn the tables on the overall work safety and well-being of humans in a complete industrial process.
This is made even more significant in light of manual blast cleaning being dangerous, strenuous, and unpleasant work. As people nowadays demand more from their work, a way to simultaneously transform an employee’s job description to be more healthy and pleasant they also stay longer. Automated robotic abrasive blasting reduces employee turnover and significantly improves work well-being. It also improves the efficiency of a single worker as time is freed for other operations. Blastman robots are truly a part of the industrial automation revolution.
You might be interested in these articles
Company News
03. Apr 2025
BLASTMAN BLAST CLEANING ROBOTS IN DIFFERENT INDUSTRIES
Blog Posts Company News
01. Apr 2025
BLASTING ROBOTS PROMISE EFFICIENCY
Blog Posts Company News
13. Mar 2025
SUPPORTING GROWTH WITH AUTOMATED BLASTING
Company News Events
03. Mar 2025
Welcome to visit us at MECSPE, Bologna from March 5th to 7th.
Blog Posts Company News
12. Feb 2025
ROBOTIC ABRASIVE BLASTING IS AN EASIER CHOICE THAN YOU MIGHT THINK
Blog Posts Company News
22. Jan 2025
LEADING THE FUTURE OF ROBOTIC BLASTING
Blog Posts Company News Events
16. Dec 2024