Leading the Future of Robotic Blasting
Leading the Future of Robotic Blasting
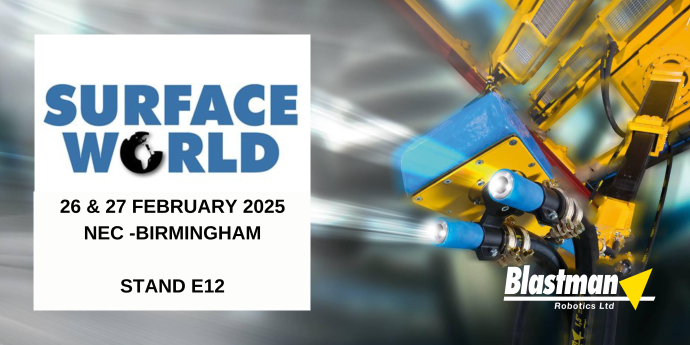
Blastman Robotics has been a global leader in industrial blast cleaning since the 1980s. Our robotic systems are used in many industries worldwide, making blasting safer, faster, and more efficient. Since then, Blastman Robotics has developed into an expert in robotic blast cleaning by offering customer solutions that fit their specific needs, whether it is a turnkey solution or retrofitting existing facilities.
Today’s Expertise
Today, Blastman Robotics is recognized as a leader in robotic blast cleaning technology. One of the main reasons for our success is that we design robots specifically for blast cleaning, instead of modifying standard industrial robots. This makes the machines much more durable and reliable in the harsh conditions of blasting rooms.
Another strength of Blastman Robotics is its ability to provide custom solutions. Every customer has different needs, and we work closely with them to design robots tailored to the job. Whether it’s cleaning large structures or smaller components, Blastman can provide a solution that works.
We have also developed our own offline programming tool called “Blastman Studio” where customers create programs based on their 3D models. Of course, robots come with the possibility to use methods like teach-in or point-to-point programming, depending on their needs. This flexibility helps ensure that our robots are not only highly effective but also user-friendly.
In addition, the robots can be programmed to automatically clean workpieces after blasting, using compressed air to remove dust and abrasive. This makes the process even more efficient and allows the blasting room to be ready for the next job.
Blastman B20S robot blasting large castings
Safer and More Efficient
One of the biggest advantages of robotic blast cleaning is that it improves safety for workers. Manual blast cleaning can be dangerous, exposing workers to dust, noise, and physical strain. By using robots, companies can remove workers from the blasting room and control the process from a distance. This reduces health risks and creates a safer working environment.
Robotic blast cleaning is also much more efficient than manual blasting. Robots can reach an efficiency of up to 200m2/h. This saves time, reduces energy use, and lowers labor costs. Robots also don’t get tired, meaning they can work continuously at high performance without breaks. This makes the entire process more cost-effective for the customer.
Transforming Blasting Operations Across the UK and Ireland
Our robots have been deployed by Alstom in Derby, UK, to clean passenger coaches, helping them maintain the high-quality standards expected in the rail industry.
Blastman systems have been instrumental for Swire in Aberdeen, Scotland, where they are utilized for blasting containers, offering both efficiency and safety for their operations.
In Ireland companies such as Liebherr in Killarney, Ireland, have experienced these benefits firsthand, using our robots for crane component blasting, where continuous operation without breaks has increased their overall productivity.
Blastman B20S and B20CS robots were installed in the existing blastroom.
Adapting to the Future
At Blastman Robotics, we’re not just focused on safety and efficiency—we’re also embracing the future with digital technology. Our fully automated blastrooms now include smart digital controls that allow real-time monitoring, easy adjustments, and preventive maintenance activities. By linking these systems to manufacturing execution systems (MES), customers can better manage their blasting processes and maximize their investment.
Our latest innovation is Robot Blastroom 4.0. This new system brings all parts of the blasting process together into one advanced solution.
Key features include:
-
Unified Control System: This system allows full control of the blasting process through one interface. It includes self-monitoring, troubleshooting, predictive maintenance, and easy connection to customer systems (MES).
-
Advanced Use of Data: The system collects and analyzes data to optimize performance, reduce maintenance needs, and ensure cost efficiency. Data related to energy and abrasive consumption, machine condition, and maintenance are monitored and reported.
-
Abrasive Handling: The system ensures a stable abrasive mix with automatic refills and monitoring. This results in less consumption, reduced wear on parts, and lower costs.
-
Ventilation: Optimized ventilation with energy-saving modes ensures dust removal and clean air while maintaining efficiency through smart controls.
-
Maintenance-Free Scraper Floor: Our heavy-duty scraper floor is designed for minimal wear, providing long-lasting durability and energy savings.
-
Room Interior: The design is optimized for both robot and manual operations, reducing maintenance costs and improving efficiency. Robot operations focus on durability, while manual operations focus on visibility and accessibility.
Overall, the Robot Blastroom 4.0 is our way of providing a safer work environment, reduced manual labor, and increased overall production efficiency.
Two wall-mounted robots and two gantry-type robots are in the blastroom blasting freight cars.
Commitment to improvement
Blastman Robotics has always been committed to improving its technology and customer service. We invest heavily in research and development to keep our robots at the top of the blast cleaning technology. Over the years, we have fine-tuned the designs and continue to make improvements based on customer feedback and technological advancements.
We value a long-term relationship with our customers. Each project is the start of a long-lasting partnership. Blastman provides ongoing support, including maintenance services and spare parts, to ensure that our robots continue to perform at a high level. This commitment to customer satisfaction has been key to Blastman’s success over the years.
Ready for the Future of Automation
As more industries embrace automation, Blastman Robotics is well-positioned to lead the way in robotic blast cleaning.
We are focused on today’s needs and the future. As the demand for automation continues to grow, the company is ready to meet the challenge with its advanced robotic systems and commitment to continuous improvement.
With decades of experience and a clear vision for the future, Blastman Robotics will remain a key player in industrial automation, helping industries around the globe transition to safer, more efficient blast cleaning.
Because Blastman is Built for Blasting.
Tuomas Heikonen
Sales Manager
Blastman Robotics Ltd
WE ARE EXHIBITING AT SURFACE WORLD - 26th & 27th February 2025
Blastman Robotics Ltd will participate in Surface World 2025, The Nec Hall 11, Birmingham, United Kingdom.
Surface World is the UK’s only event dedicated to the surface treatment, product finishing, and coatings industry. It provides a major showcase for the very latest technology and developments in this important and expanding area.
Blastman Robotics provides innovative solutions by applying the latest advanced technology to solve the challenges of blast cleaning.
Blastman robots are increasingly the number one choice for a durable and efficient blast-cleaning solution. The robot can be integrated into existing blast cleaning facilities or brand-new surface treatment lines.
Welcome to visit us! Blastman is located at Stand E12.
You might be interested in these articles
Company News
03. Apr 2025
BLASTMAN BLAST CLEANING ROBOTS IN DIFFERENT INDUSTRIES
Blog Posts Company News
01. Apr 2025
BLASTING ROBOTS PROMISE EFFICIENCY
Blog Posts Company News
13. Mar 2025
SUPPORTING GROWTH WITH AUTOMATED BLASTING
Company News Events
03. Mar 2025
Welcome to visit us at MECSPE, Bologna from March 5th to 7th.
Blog Posts Company News
12. Feb 2025
ROBOTIC ABRASIVE BLASTING IS AN EASIER CHOICE THAN YOU MIGHT THINK
Blog Posts Company News
22. Jan 2025
Leading the Future of Robotic Blasting
Blog Posts Company News Events
16. Dec 2024