Robotic Blasting with The World Leader
ROBOTIC BLASTING WITH THE WORLD LEADER – THE STORY OF BLASTMAN ROBOTICS
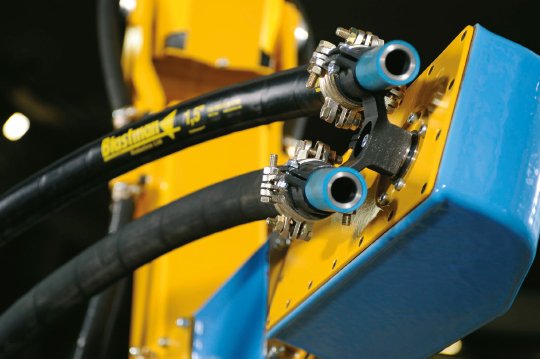
Today, Blastman Robotics' blast cleaning process is an integral part of countless industrial processes around the world, but the company's position has not come for nothing. Blastman has an intriguing history that goes back all the way to the dawn of industrial robotics.
The cornerstones of Blastman’s success in robotic blasting were laid in place early on, but the development of methods and technology didn’t end there. How did all of this happen and what are the ingredients of Blastman’s success story? Read the whole article and find out.
Additionally, you can also jump to the most interesting section straight from here:
- Abrasive blast cleaning in a nutshell
- Blast from the past
- Roots solid as steel
- How a success story is forged
- Today’s leading expert in robotic blasting
- Robotic blasting with broad shoulders
- Leading technology in robotic blasting – read why Blastman is the no. 1
- The future of abrasive blasting is here but still evolving
- The fewer people in blasting chambers, the better
Abrasive blast cleaning in a nutshell
Abrasive blasting (often referred to as sandblasting) is a method of propelling a high-pressured stream of abrasive material against a surface to smooth, roughen, or shape it or to remove surface materials such as remnants of paint coating. The abrasive material is usually propelled with pressurized fluid, such as compressed air or a centrifugal wheel. The first abrasive blasting processes originated as far back as the late 1800s.
The blasting process can utilize many materials, from highly abrasive (metal and sand) to mildly abrasive (soda and dry ice). It can also be roughly divided into manual or automated methods, the latter of which is becoming increasingly common. In this method, the workpiece is handled inside a blasting room by robots and a variety of other automated solutions.
Blast from the past
In the early 1980s, the now-extinct Finnish heavy industry company Tampella was very much alive and kicking. Among other things, it manufactured machinery for harsh environments but had a lot of problems with its blasting station. Challenges with occupational safety eventually led the factory doctor to urge the management to invest in a solution that would free the workers from operating inside the blasting station.
This led to a group of approximately 20 engineers putting their heads together and setting out to develop a robot capable of operating in challenging conditions inside the blasting station. At the time, practically the only usable technology was hydraulics. Luckily, though, Tampella’s mining industry branch, Tamrock, had strong expertise in the field.
Embarking on this mission can nowadays be viewed as the starting point of Blastman Robotics and, thus, robotic blasting. Completing the first robots required a lot of basic development work, which in turn required a lot of resources. This was only possible within a large corporation such as Tampella. In 1985, the first commercial blast cleaning robot with an automated control system and programming capabilities was proudly delivered to Valmet.
Roots solid as steel
The other root of Blastman’s family tree leads to the famous Finnish steel mill, Rautaruukki. In the ’80s, the mill had its own engineering department that executed projects for its own factories. Within the engineering team operated a group called Aumek. As Rautaruukki built its own factories, the group gained experience and know-how that would later prove essential.
In one of its export projects, Rautaruukki Engineering delivered an abrasive blasting line for the surface treatment of sea containers in Siberia, and Aumek was heavily involved. By this time, Tampella had developed robotic products, and one was decided to be fitted for blasting the inner surfaces of the containers. This effectively made the project a joint effort.
After the project, Aumek oriented itself to surface treatment projects. Rautaruukki and Tampella actually ended up competing over a number of projects until Rautaruukki purchased Tampella's robotics business. As is now evident, this marked a significant turning point in the story of a certain future company in robotic blasting.
How a success story is forged
The blast cleaning robot was initially only a product of Rautaruukki Engineering. At some point, the businesses decided to be separated, and a surface treatment group was founded within Rautaruukki Engineering. The group consisted of many employees who later served long careers at Blastman.
In 1997, Rautaruukki decided to focus on its core business, steel production, and a window of opportunity opened. A management buyout took place, and Pentti Salonen, who would become the long-lasting CEO, established Blastman Robotics.
In the beginning, Blastman had challenges in its sales efforts. Since industrial automation and robotization were in their infancy and faced a lot of fear and preconception, practically every selling process was a mountain to climb. On the other hand, Blastman had a mountain to back it up as well, as from the client’s point of view, the purchase was made from Rautaruukki and not just some small and yet nameless company.
Additionally, Blastman had people with a history in the sales of Rautaruukki and knowledge of the purchasing process of a big company. This proved invaluable also through experience in contractual law, making it possible for Blastman to take greater risks while keeping them under control. This, of course, was useful for the customers as well.
Another factor in Blastman's jumpstart was how it differed from many other companies in its extremely strong project expertise. As Rautaruukki Engineering had already been a project organization, Blastman was immediately able to execute export projects—at first to Germany and eventually globally.
The sales and marketing efforts of Blastman's robotic blasting solutions were, in fact, purposefully aimed at big companies known to be able to make heavy investments but also have enough production capacity to make the investments profitable. This way, regardless of the initial challenges, Blastman’s strength from the get-go was, and still is, its clientele of big companies.
Maintenance of Blastman B20S to guarantee smooth robotic blasting.
Today’s leading expert in robotic blasting
Since the founding of Blastman Robotics, the market mentality towards automation has shifted from reserved to striving. Whereas in the beginning, there was a heavy burden of proof on how robotic blasting—and automating industrial machinery in general—was even a possibility, Blastman now has solid evidence and working references on various industrial sectors worldwide.
One of the cornerstones of this success is the time well spent since the robotic departure from Tampella—decades of first-hand experience in blast cleaning technology and its automation.
In recent years, Blastman has experienced a generational change as many of the old guards have retired and are followed by younger blood. Blastman also does educational cooperation, especially through thesis and diploma thesis work, and some of these students get recruited, too. A lot of time has gone by since the original design and development process, and many of the original experts have departed, but on the other hand, the knowledge is somewhat in the technology.
Additionally, instead of hanging the newcomers out to dry, the know-how and methods have been successfully passed on with smart mentoring. The characteristic project expertise has stayed in the picture and, combined with modern education in engineering and automation, has taken Blastman’s competence to a new level.
The shift is not only natural but essential, as the same shift has been ongoing in Blastman's customer organizations as well. Selling and buying communication methods have changed and are carried out through a new kind of dialogue. Just like Blastman is invested in keeping its technology cutting edge, the same goes for its ability to communicate and cooperate.
Robotic blasting with broad shoulders
To this day, Blastman Robotics follows the principle of the late Pentti Salonen, stating that a deal should mean not only a purchase order and delivery but also the beginning of a long-lasting partnership. This is extremely important since blast cleaning equipment depends on its provider after installation.
When this is reflected in the decades-long lifespan necessary for a blast cleaning line, Blastman’s well-known reputation in the industry has created an advantage. When a potential client gets an offer from a small local company, for example, it begs the legitimate question of whether that company is going to be around for the next decade or two.
Blastman is devoted to caring for its customers and supporting their operations, for example, by providing maintenance service and consumable components. The company feels the need to prove every day that its customers get what they have been promised, and even that can be developed further.
Leading technology in robotic blasting – read why Blastman is the no. 1
The basic concept and methods of robotic blasting have remained unchanged for a very long time which is due to the harsh environment and the process itself being destructive. Robotics consists of modules that can be utilized for various industrial needs. Thanks to its broad clientele, Blastman has accumulated a lot of experience and can thus provide even better solutions in return.
One of the competitive advantages of Blastman Robotics is that the company designs and manufactures its own robots specifically for the demands of the blasting process. This means that, unlike some competitors, it doesn’t use normal industrial robots that cannot withstand the conditions of a blasting room to the same extent and are, unfortunately, expensive to repair.
In addition, Blastman is able to provide customer-specific, tailor-made solutions. Of course, the basic concept of its robotics is pretty much constant, but it is always fitted to the needs, and the control system is built to the customer's specifications.
Blastman’s customer projects are divided pretty early on between normal and special. Normal projects, too, have a lot of wiggle room but concern the kind of changes that can be prepared for in advance. Special projects, in turn, require more extensive customization and usually last longer. Special requests are handled during sales and usually concern accessories and added features. Challenging projects are not a cause for concern either when one can trust the technology.
3D model of a robotic blasting chamber with Blastman B20S robot
Customers typically provide Blastman with a 3D model of their workpiece, based on which the dimensions can be implemented. Lacking a model is not an obstacle to moving forward with a project since the modelling can also be done for the customer.
The future of abrasive blasting is here but still evolving
Blastman is not only a robotics manufacturer but also a provider of comprehensive automation solutions. Compared to simple robotics or software suppliers, the difference is in how Blastman is able to handle the entirety of the customer's process and provide true automation for such a challenging job as abrasive blasting. The level of automation inside the blasting room of Blastman Robotics is ever-growing and enables, for example, different measurements during blasting. A fully automated room is also more cost-efficient for the customer.
An example of Blastman’s dedication to continuous improvement is two facilities that customers use in actual production and that were built in cooperation with them. This allows the company to run tests or provide a customer with a chance to familiarize themselves with and become convinced of robotic blasting.
One of Blastman’s advantages is that the automation of abrasive blasting is somewhat a niche and there is practically no research information about it, unlike for example welding automation. Meanwhile, Blastman has strong experience and research data on what withstands the gruelling conditions of abrasive blasting.
Unlike any other automation provider, Blastman considers manual abrasive blasting its truest competition. This mentality, however, doesn’t stem solely from a business point of view. Because of its roots in the invention that would save countless people from the strain and dangers of manual blasting, the company only wishes for the shift to accelerate.
The fewer people in blasting chambers, the better.
The outbreak of COVID-19 has naturally caused global uncertainty. However, as the market is examined through adversities, interest in automated robotic blasting is growing still, not least because of work safety. This trend is not likely to change.
Abrasive blasting hasn’t always represented cutting-edge technology. Blastman is proud to have taken the method there, aims to keep it that way, and hopes to advance the awareness of its high-end usability. To follow progress or to lead it are two completely different things.
Check out our references and products.
You might be interested in these articles
Blog Posts Company News
03. Jul 2025
BLAST CLEANING SOLUTIONS FROM KEMPELE* TO BRAZIL
Blog Posts Company News
17. Jun 2025
WHICH ROBOTIC BLAST CLEANING SYSTEM IS RIGHT FOR YOU?
Blog Posts Company News
31. May 2025
BLAST CLEANING METALWORKING MACHINERY
Blog Posts Company News
13. May 2025
BUILT TO BLAST - HOW TO MAKE ROBOTS LAST FOR DECADES
Company News
03. Apr 2025
BLASTMAN BLAST CLEANING ROBOTS IN DIFFERENT INDUSTRIES
Blog Posts Company News
01. Apr 2025
BLASTING ROBOTS PROMISE EFFICIENCY
Blog Posts Company News
13. Mar 2025