ROBOTIC VS MANUAL BLASTING CHAMBERS
ROBOTIC VS MANUAL BLASTING CHAMBERS
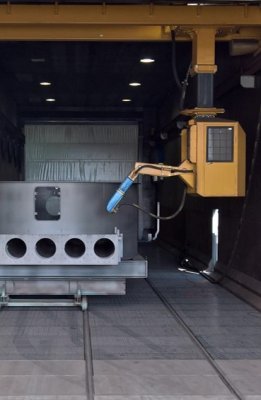
Blast cleaning large metal structures such as crane components or railway vehicles is a very demanding and tiring process that manual blasters typically do. For these applications, special robots and correspondingly durable blasting chambers have been developed which achieve significantly higher efficiency.
Blasting is the dominant method when it comes to the pre-treatment of large metal structures before applying coatings but is a tedious and dangerous process. With specially designed blast cleaning robots with high blasting power, such work can be conducted faster and safer, as well as more economically and with higher quality.
Faster and safer
Manual blast cleaning of large metal structures needs a lot of effort, as workers are exposed to high physical stress, noise, and dust in a hazardous environment. The major advantage of blasting robots is that they are inexhaustible, even at high output rates. They could achieve a blasting performance of over 200 m²/hour, while a worker is unable to manage even 15 m²/hour. Operators of robotic blasting chambers work comfortably within a control cabin or control room, where they are protected from the hazardous environment. As with many of today’s machines and devices, the blasting robot is easily operated with joysticks and a touch panel.
Operators work comfortably within a control room
More economically
To illustrate the advantages, the blast cleaning of an average passenger coach of the railway industry is given here as an example. Four manual blast cleaners need about two shifts for such a passenger coach, while a blasting robot makes this possible in less than one shift. As a result, the entire ventilation and abrasive reclaim system of the blasting chamber only must be in operation for half as long, and the lighting can even remain completely switched off, as the robot does not require any light. Depending on the size of the blasting chamber, this saves approx. 500-600 kWh of energy and 50-60 hours of labor costs per wagon.
After blasting, the robot can also automatically clean the workpiece of abrasive residue and dust with compressed air, which further improves the process efficiency. The component is thus available for the next work step more quickly and the blasting chamber can also be occupied again sooner. For most blasting applications, the processing costs per square meter with a robotic blasting chamber are about half those of a manual one, which often results in a return on investment (ROI) of less than 2 years.
Higher quality
An 8-axis gantry-type robot can reach all areas of the blasting chamber and therefore, could reproducibly treat the workpiece surfaces with the optimal blast cleaning distance and angle. Blast cleaning robots from Blastman Robotics do this without any problems when blasting underbodies of e.g., passenger coaches or even roofs without scaffolding at great heights. In series production, the robot repeatedly performs the programmed work sequences, and thus reliably delivers reproducible cleaning results without human errors. With the integrated simulation tool for the visual representation of the blasting process, possible collisions can also be identified, and the blasting programs further optimized.
Metal structure before and after robotic blast cleaning.
Durable solution
Since blast-cleaning robots have a significantly higher blasting performance, more powerful and durable blasting chambers are required. This is achieved by appropriate ventilation and blasting media systems that can process larger quantities of air and abrasives. The blasting chambers are constructed with solid steel frames to manage the static and dynamic loads and forces of the robots. Furthermore, Blastman Robotics' blasting chambers are built with sandwich panels at least 100 mm thick, which are filled with Rockwool and coated with up to 10 mm glued rubber granulate. This reduces the noise level of the application and significantly extends its lifetime.
Digital networking
As blasting robots uses and creates digital data, they could easily be integrated into smart blast rooms with digital process control and reporting, which could straightforwardly be connected to the manufacturing execution systems (MES) to meet the requirements of Industry 4.0. Currently, the EU and many nations are generously funding projects for digital transformation and energy saving. With the investment in a robotic blasting chamber that uses and creates digital data, and saves energy due to the significantly faster processing, there is a high probability of funding.
Heiko Reski
Sales Manager
Blastman Robotics Ltd
You might be interested in these articles
Company News
03. Apr 2025
BLASTMAN BLAST CLEANING ROBOTS IN DIFFERENT INDUSTRIES
Blog Posts Company News
01. Apr 2025
BLASTING ROBOTS PROMISE EFFICIENCY
Blog Posts Company News
13. Mar 2025
SUPPORTING GROWTH WITH AUTOMATED BLASTING
Company News Events
03. Mar 2025
Welcome to visit us at MECSPE, Bologna from March 5th to 7th.
Blog Posts Company News
12. Feb 2025
ROBOTIC ABRASIVE BLASTING IS AN EASIER CHOICE THAN YOU MIGHT THINK
Blog Posts Company News
22. Jan 2025
Leading the Future of Robotic Blasting
Blog Posts Company News Events
16. Dec 2024