TECHNICAL REPORT - BLASTING ROBOTS INCREASE EFFICIENCY
TECHNICAL REPORT - BLASTING ROBOTS INCREASE EFFICIENCY
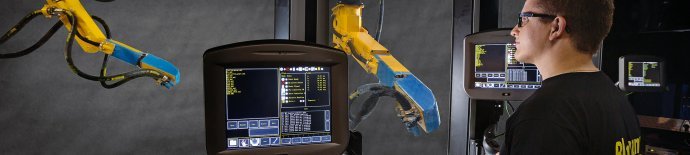
The original way blasting robots proved their efficiency compared to other blasting methods has hardly changed over the years. Larger nozzles and hoses enable larger blasting streams and amount of blasting material. This principle remains, but the advantages of robotic blasting do not end there.
There has been and is continuous development in the field of blasting robots. The level of programming and the competence in application and maintenance have been further developed, improving the already impressive reliability and durability of the equipment. As a result, the overall efficiency of the blasting process has been continuously increased, making processing not only faster and safer overall, but also more cost-effective and with higher quality.
Modern blasting robot for automatic blasting
Man and machine
To this day, robots have a certain mystique attached to them and it is common to compare their capabilities with those of us humans. When it comes to industrial robots, the comparison is often associated with the fear of humans gradually being replaced. But if we are honest, throughout our existence we humans have invented and developed tools to make our work and lives easier. At the end of the day, even sophisticated robots are just tools, and sometimes it is not only wise but downright necessary to leave certain tasks to them. For this reason, blasting robots are not a threat, but a value-adding addition.
Manual blast cleaners must endure very harsh and strenuous conditions, while robots can process the components without fatigue, without breaks, and with reproducible quality. In addition, a robot requires little space. It can directly process the interior and underside of many components, which it is ergonomically unfavorable for humans or impossible without turning the component. In addition, robots can be mounted on gantries with telescopes to blast XXL components at great heights. This eliminates the need for working platforms or the erection of scaffolding and ladders. The robot-based blasting process can often be realized in such a way that the entire component is cleaned in one shot.
The use of blasting robots improves work safety enormously and also has a positive effect on human resources. Manual blasting workers are becoming increasingly difficult to find and usually only perform this grueling job briefly before seeking easier employment. However, if they are offered the opportunity to switch to operating robots, they tend to stay with the company many times longer. The use of blasting robots not only reduces employee fluctuation but also reduces the number of sick days in the company - in other words: the back pain goes - the know-how stays.
Simple operation of the blasting robots from the control room.
Increased productivity and reproducible quality
The most important reason for replacing manual blasting with robots, apart from the human aspect, is of course productivity. When industrial processes are analyzed, it is inevitably about facts and figures. While manual workers can only use one small to medium-sized blasting nozzle with a maximum of 7 bar blasting pressure at a time, modern blasting robots use two large nozzles with up to 10 bar blasting pressure. Depending on the application, blasting capacities of over 200 m2 per hour can be achieved, while a blasting worker achieves just 15 m2 per hour for the same application.
Blast wheel turbines achieve throw-off speeds of 50 to 100 m/s. However, to keep their wear within limits, they must mainly use large, rounded blasting particles. Blast cleaning robots, on the other hand, can use all types of abrasives in all grain sizes and shapes and achieve particle speeds of up to 200 m/s. This not only cleans the workpiece faster but also gives it a finer structure with many small peaks, which has a positive effect on the adhesion of the coating to be applied. In addition, small particles have a lower consumption rate because they do not break as quickly.
Multi-axis blasting robots that reach all areas of the blasting chamber also have the advantage that they can always process the components with the optimum blasting distance and blasting angle. This gives the workpiece a uniform blasting pattern with the desired degree of preparation everywhere with reliable repeatability. Together with the high particle speed, this increases the resistance of the workpiece surfaces - important for machine components and e-mobility. In addition, the robot can use compressed air to remove abrasive residues and dust from the component after processing, which means that downstream processes can be carried out more quickly.
Optimum blast cleaning even in areas that are difficult to reach.
Innovative software enables intuitive programming
Components with complicated geometries require complex motion sequences of robot-based blasting processing. Innovative software tools such as "Blastman Studio" enable the intuitive programming of motion paths and thus efficient program generation without interrupting production or having to write a line of code yourself. The CAD data of the components can be easily imported into the software’s 3D simulation environment. From this, the sequences of individual robot movements are automatically created via drag and drop. The integrated simulation tool for a visual representation of the blasting process can also be used to identify potential collisions and optimize the blasting programs in advance. The digital data from the robot-based blasting processing can also be used by higher-level master computers to control and monitor production by Industry 4.0.
Improved economic efficiency
In the meantime, a wide variety of designs are available, ranging from simple stand-alone solutions to 8-axis gantry robots and mobile blasting robots. This opens up unique possibilities that can be optimally adapted to the customer's applications and requirements. Blast cleaning robots not only increase productivity and ensure the quality of surface pretreatment, but they also minimize energy and material consumption and open up additional optimization potential. For example, the return on investment for many blasting robot installations is achieved after just a few months. Added to this are the additional revenues from increased production.
Heiko Reski
Sales Manager
Blastman Robotics Ltd
You might be interested in these articles
Blog Posts Company News
17. Jun 2025
WHICH ROBOTIC BLAST CLEANING SYSTEM IS RIGHT FOR YOU?
Blog Posts Company News
31. May 2025
BLAST CLEANING METALWORKING MACHINERY
Blog Posts Company News
13. May 2025
BUILT TO BLAST - HOW TO MAKE ROBOTS LAST FOR DECADES
Company News
03. Apr 2025
BLASTMAN BLAST CLEANING ROBOTS IN DIFFERENT INDUSTRIES
Blog Posts Company News
01. Apr 2025
BLASTING ROBOTS PROMISE EFFICIENCY
Blog Posts Company News
13. Mar 2025
SUPPORTING GROWTH WITH AUTOMATED BLASTING
Company News Events
03. Mar 2025